برای نگه داشتن نوارها علاوه بر چسب، از میخ نازک استفاده کردیم. این مهم است، شما می خواهید هر قطعه به طور دائمی متصل شود تا هنگام قالب گیری از هم جدا نشود.
ما صفحه پشت کیلومتر اصلی را بالای ابرو قرار دادیم و شکل را ترسیم کردیم.
با استفاده از سنباده تسمه ای لبه عمودی (با چرخاندن یک سنباده افقی قدیمی در کناره آن را درست کردیم و پایه های جدیدی درست کردیم) شکل ابروی بالایی را شکل دادیم. یک سنباده افقی معمولی نیز کار می کند، اما ما دریافتیم که کنترل قسمت خود از این طریق آسان تر است.
برای تکمیل طراحی، یک قطعه تریم پایین تر ساختیم تا یک فرورفتگی مرکزی برای گیج ها ایجاد کنیم. توجه داشته باشید که چگونه فضای اطراف گیج ماکت وجود دارد. این برای قرار دادن پلاستیک است. ما تمام لبه ها را با یک لقمه گرد پخ کردیم.
تمام سطوح ناهموار را با بتونه سنگی صاف کردیم و سپس با کاغذ 80 سنباده زدیم. شما می خواهید انتقال صاف و بدون حفره یا خطوط موج دار باشد. پلاستیک خراش را نشان نمی دهد، اما قطعاً ایرادات را نشان می دهد.
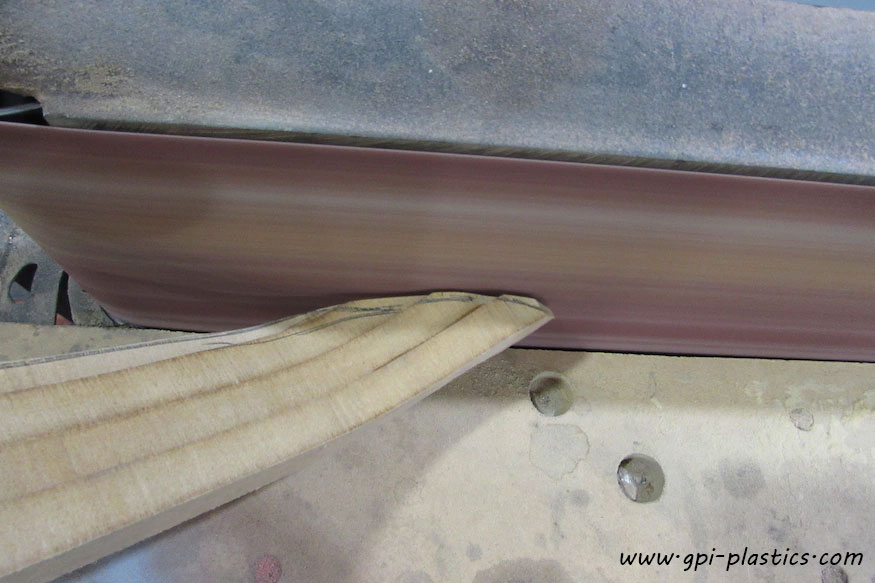
با استفاده از دلردرناحیه ابرو ، دو مورد از محل نصب پیچ اولیه را اضافه کردیم. اینها باید بزرگتر از نسخه اصلی باشند. اگر دقت کنید، سوراخ هایی را در امتداد تمام گوشه های فرورفته مشاهده خواهید کرد. این سوراخهای خلاء هستند که برای بیرون کشیدن هوا استفاده میشوند، به طوری که پلاستیک به شکل محکم در الگو قرار میگیرد.
توجه داشته باشید که چگونه پایه پهن تر از قسمت بالایی است. ما همچنین کل الگو را روی یک تکه ام دی اف دیگر گذاشتیم تا مقدار زیادی گوشت به ما بدهد تا قسمت نهایی را متناسب با آن شکل دهیم.
در حالی که ما از یک ماشین تجاری برای تشکیل این قطعه استفاده می کنیم، این دستگاه کوچک ساخت ما است. ما آن را با کمتر از 10 میلیون ساختیم و صفحه (پایه تشکیل دهنده) 20 سانتی متر است. این دستگاه از یک المنت در قسمت بالایی استفاده می کند و سینی پلاستیکی روی صفحه بالا و پایین می رود. ماشین های تجاری دارای سینی های صفحه متحرکی هستند که قطعه را به داخل پلاستیک فشار می دهد.
ما الگو را روی صفحه قرار دادیم و یک ورقه پلاستیکی باریک را در سینی قرار دادیم. به طور معمول، این الگو روی برخی از واشرها قرار می گیرد تا لبه زیرین واضحی داشته باشد.
بعد از برش دور با اره نواری، از سنباده نواری برای شکل دادن به قطعه استفاده می کنیم.
جای گیج ها را برش دادیم و قسمت را برای رنگ خراشیدیم. بسته به پروژه خود، می توانید قسمت صاف پلاستیکی را بیرون بکشید یا بافت داشته باشید. ما یکی از هر کدام را کشیدیم، اما سمت صاف برای این پروژه بهترین به نظر می رسد.
پس از تکمیل کار، قطعه خود را با رنگ سبز رنگ کردیم.